I’ve had a parabolic dish I bought off Ebay sitting around for the better part of a year. The whole idea was to build a parabolic mic out of it based on the dishes from Telinga, but for one reason or another I got stuck in the design-and-abandon phase and never got to the just-cut-metal phase. So the dish sat, collected dust, and didn’t do much except confuse my cats and annoy my family.
At some point in there I picked up eight EM-172 capsules in two matched sets of four from FEL Communications aka Mic Booster along with a bunch of yoga blocks. My plan with these was to make a pair of quad capsule foam SASS arrays similar to Vicki Powys’s for recording surround sound. I got stuck in design-and-abandon on this project, too.
In the end, though, it all worked out for the best because of yet another project. Only, this one actually reached completion, mostly because I was doing it for someone else. (There’s nothing like a deadline for getting a designer off top dead center.) The project involved designing and 3D printing some mating threaded parts. I modeled the threads in CAD, put the clearance into the model, and printed the parts. The threads meshed first try. W00t!
That was reason enough to celebrate, but it was also reason to scratch my chin and go, “Hmmm!” Being able to 3D print threads solved one of my issues with the parabolic mic: how to attach the handle to the dish. While reading this article from Avesrares on a DIY parabolic dish I had my second epiphany: Their stereo parabolic mic used four matched EM-172 capsules… just like the ones I had sitting in an envelope. Thank goodness I hadn’t built those SASS arrays, either!
So with technique and components in hand, I set about making my own stereo parabolic mic.
The Dish
One difference between my DIY parabolic mic project and many others is that I made no attempt to fabricate my own dish. There’s an Ebay seller who makes 22″ Lexan dishes for under $50USD. Shipping to Hawaii was expensive, but the dish itself was pretty affordable. This was where the whole project started.
The Handle
I like how the Telinga handles attach to their mics. The Avesrares article mentioned using auxiliary drill handles in a similar fashion, so I searched Ebay and found one of a suitable size for under $10US. The next step was to model a corresponding threaded tube and two screw plates to attach the handle to the dish.
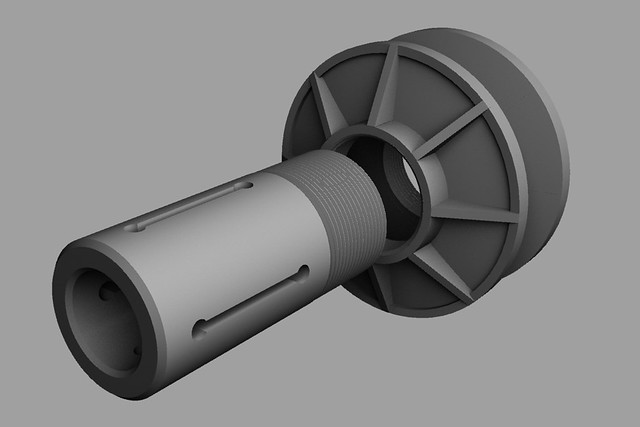
I wanted to be able to build interchangeable microphones, so I sized the inside diameter to take 3/4″ schedule 40 PVC pipe. The screw plates are 4″ in diameter – about the maximum my 3D printer can handle. The screw pitch is 14 TPI (sorry, metric system), and was sized to fit the outside diameter of the tube. If I remember right the threads left 10% flats top and bottom, and I left 0.020″ clearance between the tube and the screw plates. (They meshed great, too. W00t!)
Since these are sandwiching a parabolic form, the inner surfaces of the screw plates are curved to match. I added a layer of craft foam inside and out in an effort to provide some damping for handling noise (which it didn’t) and to make a nice snug fit (which it did.) Everything went together fine.

The Microphone
In an article written by Klas Strandberg from Telinga Microphones, he explains that the focus of an acoustic paraboloid isn’t a precise affair. The mathematical focus of the paraboloid will be the point of best focus, but the size of the region of focus is frequency-dependent. I’d try to paraphrase here, but the article puts it so well there’s really no point. If you’re interested, read his article.
The upshot is that you can, to some degree, adjust the EQ of a parabolic mic by shifting where the capsules are with respect to the point of best focus. I knew I wanted some latitude, but I didn’t know how much range I might need. So I cut the 3/4″ PVC pipe a little long, reasoning I could always cut it down later.
One bonus to using 3/4″ PVC pipe is that Neutrik XLR connectors are a nice snug press fit into the tube. Since I was planning to make a stereo microphone, and since I’d already built an XLR-5 to twin XLR-3 splitter cable for my MS Alice microphone, I used an XLR-5 connector for this mic as well. While not the most elegant setup for this connector, it was an expedient solution that let me get on with the business of building the rest of the microphone. I can always revisit this later.
(As a quick aside, “I can revisit this later” is designer code for “You’re going to see this in the final version.”)

My first design for the business end of the microphone followed the logic in the Avesrares article: a baffle that splits the dish left-from-right and a second baffle facing the dish. Unfortunately my dish has a shorter focal length than its depth, so adding the second baffle would’ve cut off about half the surface area of the dish.
Instead I went with a baffle similar to the one used on the Telinga microphones, except that instead of using the microphone capsules as pressure zone transducers (PZT), I stuck to familiar territory and arranged them as boundary mics. I’m not 100% sure this was an ideal approach since it moves the diaphragms of the capsules away from the axis of the dish, limiting how close they can get to the point of best focus in the radial direction. Still, it worked.

Originally I’d intended to make solid baffle plates on the 3D printer, but these would’ve been costly in terms of material and time. Instead I took a tip from the SASS I built and made them only 1mm thick. This made for a very thin, unfortunately flexible plate with a high resonant frequency. I backed it with Dynamat, which does an excellent job of damping vibrations, and sandwiched dense latex foam between the two plates to provide further damping. The whole stack wound up being acoustically dead to handling noise. (But more on the handling noise later.)
Unfortunately, before I took any pictures of the finished parts I stuck open celled foam on either plate to provide wind protection. So the only photos I have look like a big foam lollipop.

I wired the capsules using the same pattern as Vicki Powys’s SASS, except instead of wiring them into a 3.5mm TRS plug, I wired them into the XLR-5 connector using David McGriffy’s and Ricardo Lee’s Simple P48 circuit. Tuning the resistor for the Simple P48 circuit took some experimentation since each circuit was now driving two capsules instead of one. I’d quote the value of the resistors I wound up using, but there’s really no point. If you choose to build one of these, best to tune the resistors to get the bias voltage you want for your capsules.
With everything closed up, the microphone slides into the clamp tube on the dish and locks into place by twisting the drill handle. Voila, the DIY stereo parabolic microphone.

The Bling:
With such a narrow pattern microphone, I erroneously thought I’d need some way to aim it. (I’ve since used it in the field enough to know you aim these things by ear and not by eye.) One of the remnants of a previous project of mine, the camera helmet, was the small reflex sight I’d used for aiming the cameras. I mounted a short length of Weaver rail to the drill handle using a 3D printed adapter, and clamped the reflex sight to the rail. Voila, a neat looking, but ultimately useless addition to the parabolic mic.
This was rendered even more useless by the next bit of bling.

Wind Protection:
After some initial testing in the field, I found I wanted the option of another layer of wind protection. The foam on the lollipop was nice, but it wasn’t really enough to stop the kind of wind you get outdoors. (Foam is never enough to stop real wind. Like ever. Eventually I will learn.)
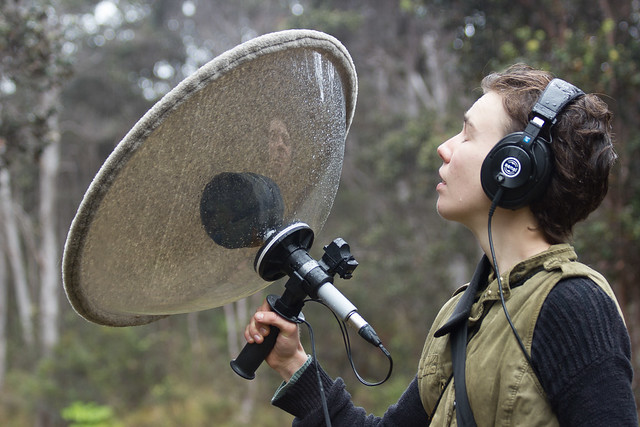
Chris Owens wrote a really good article describing the wind protection he made for his Telinga parabolic mic. I followed his directions to the letter and wound up with a very serviceable (and machine-washable!) cover for my mic.
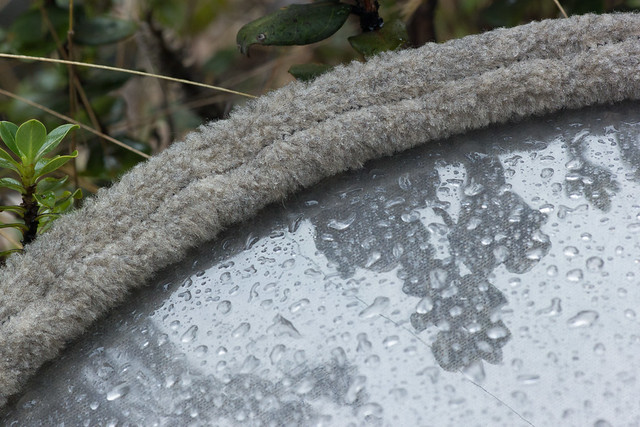
He used his dish to measure a circle of cloth, and rolled a hem at the edge that holds a length of shock cord. Once the hem is finished, the shock cord is pulled tight(ish) and is tied off. Chris Owens cautioned not to pull the shock cord too tight or the dish will warp. I made mine just snug enough to make sure the cloth stays on unless I’m ready to pull it off.
Post Script:
Now that I’ve had the chance to use my dish in the field I’ve found a number of shortcomings I’m planning to address in the future:
- Anything you can’t put a shoulder strap on is lame – My dish is incredibly awkward to carry on a trail. Klas at Telinga solved this by making 1mm thick dishes that can be rolled up and carried in a shoulder bag. I’m sticking with my dish, but I have to add a shoulder strap. This is irritating.
- Handles that can twist bother me – The drill handle I chose tightens (and loosens!) by twisting the handle. I’ve had it try to come undone in the field a couple of times when turning the dish. I’m planning to replace mine with a Bosch handle that uses a thumbscrew.
- Handling noise is lame – I’ve been chasing handling noise on the BM-*00 conversion mics I’ve been building with some success, but this thing has it twice as bad. You can’t just shock-isolate the capsules. You have to shock-isolate the dish as well because it basically acts like a great big sounding board. Anything that’ll conduct handling noise to the dish shows up in the recording. A cushioned handle like the ones on the Telinga dishes would be a step in the right direction. For now I’m wearing gloves any time I use it.
- I’m not 100% happy with the mic setup – The first prototype mock-up I did with this dish involved mounting my Alice M-S at the focal point of the dish. This worked way better than I suspected, and provided a better stereo image and a better mono image than the mic I’ve got in there right now. I’m thinking of recovering my four EM-172 capsules so I can go ahead and build that SASS surround mic, and building a dedicated mid-side mic to live in the dish.
And now for the rest…
First, A Sob Story:
I like to include audio samples in my build articles. Unfortunately I can’t for this one. Not yet, anyway. A little over a week ago I got some kind of outer ear infection in both ears. The tinnitus I’ve experienced for the last twelve years or so is about a bazillion times worse at the moment, and my right ear has lost about half its frequency range. I tried to edit a recording I’d made of a katydid and realized I couldn’t even hear the katydid in that ear. (And it’s not like they’re subtle or anything.) Even worse, my two ears currently hear broad-spectrum noise as two completely different sounds. Until this infection clears up, my ears are screwed. I can record, but I can’t edit. Sorry.
Second, A Note on the Photos and a Thank You:
No, that’s not me holding the mic in the field. I was the one tripping the shutter. (I know which end of the camera I like to stay on.)
About half the pictures in this set involve wet gear. This is one of the hazards of recording in Hawaii: it rains. Rain is not ideal for recording with a parabolic mic. Each rain drop on the dish was picked up by the mic, and there were plenty of rain drops. I did make some recordings during the photo session, but because of the rain none of them really showed off the mic very well. Everything survived fine, though.
The black audio bag worn by the recordist in the photos is the brainchild of Andrew Jones, described in an article he wrote on WAV.REPORT, Tutorial: “DIY” Audio Drop Bag. Mine’s only about half finished (it still zips shut) but it’s a really good article and an unbeatable bag for the price. Thanks, Andrew!
Edit:
At the request of Benoît, I’ve made the STL files for my parabolic mic build available on Thingiverse. I’ll add them to Shapeways in the not too distant future as well, but for now they’re at least available:
Thingiverse
Cheers!